
Why do I struggle with UV ink adhesion?
Here is a statement of fact: UV printers can print on almost any material, but that doesn’t mean the ink will ADHERE WELL to all materials. Unfortunately, some printer owners continually struggle with ink adhesion or they will avoid “tough to print” materials altogether. STOP DOING THAT!
The surface tension or dyne level of certain materials make it difficult for the ink to stick. Adjusting the surface tension through a process of steps – like a wipe on adhesion promoter or flame treatment system – is what ultimately yields proper adhesion and the durability print operators strive for.
Common “tough to print” materials include glass, stainless steel, and ceramic.
When should I consider flame treatment for ink adhesion?
If looking for speed and consistency, then consider an automated flame treatment for adhesion. Printing pint glasses? Then you’ll be looking for a flame treater specifically designed for cylindrical items like the PYROBOND 4 GL. If printing to stainless steel signs, then a flatbed flame treater like the PYROTRACK would fit your needs.
Not only can you use Pyrosil and/or flame treatment for adhesion on systems like this, but the systems easily accommodate many different shapes and sizes which can make it a versatile piece of equipment in your facility. Plus, easy-to-adjust settings make it viable for many of the tough to print materials mentioned earlier.
Does a UV ink adhesion promoter really work?
Definitely! It’s a simple method that many operators use on a daily basis. It’s easy to manually apply the adhesion promoter or primer for your specific material by hand and then move on to the printing.
However, speed and the manual nature of applying the promoter can cause a shift in results from operator-to-operator or day-to-day. Operators must be consistent in their application every single time and take the necessary safety precautions when handling these chemicals.
Can my UV printer do this for me?
Furthermore, some printer models allow for the uv ink adhesion promoter or primer to be jetted through the print head. It’s a popular option as application pf the primer becomes more consistent. Plus, the system only applies the chemical where it is needed. However, jetting the primer can sometimes slow down traditional production times due to adding another ink channel to the printing cycle. It is something that print operators must weigh when making the best decisions for their process and print demand.
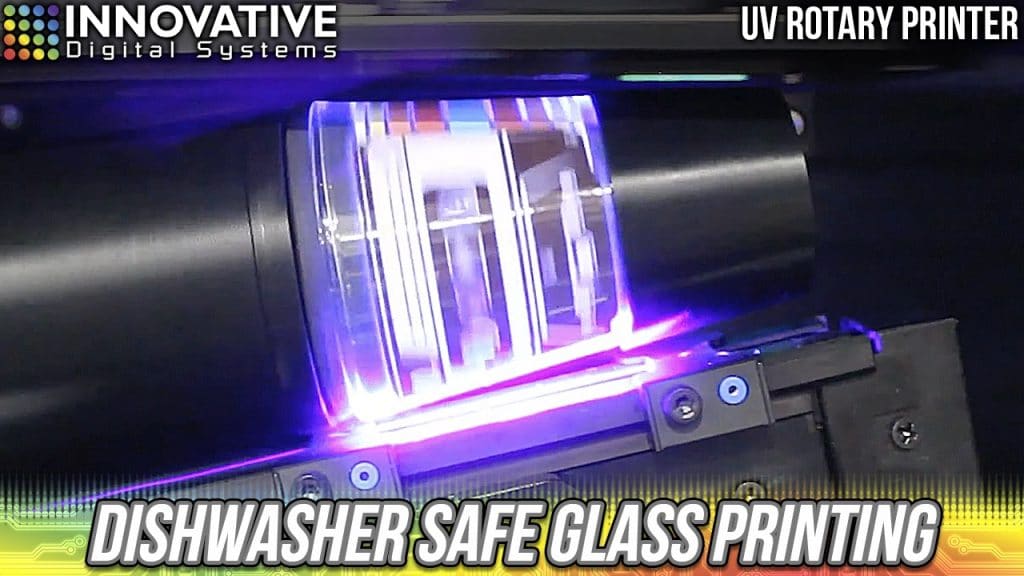
Tape test for ink adhesion and other options.
There are a couple of different ways to go about this. For starters, there’s the standard ASTM tape test for ink adhesion that many folks employ. It’s a simple method for scratching or scoring the ink and then using a specified tape to see if the scratched ink fails.
Then there’s the “real world” test. Printing baseball bats? Then print them and then hit some baseballs. Printing glass drinkware? Then print them and place them in the dishwasher. Printing signs for hospitals? Then print them and use the same cleaning solutions they would employ once installed.
One short bit of advice for your testing: Print multiple options with and without primer or a set with varying levels of varnish ink. Make sure they are labeled or coded correctly so you know which one(s) work best.
Still struggling with UV ink adhesion?
Contact the IDS print experts and we can help guide you towards the best promoter or flame treater for your business.
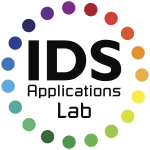
Let's Chat about your uv ink adhesion problems
Call Us Today!
Do you have questions about ink adhesion and which solution could be best for your business?
IDS print experts can answer your questions relating to technical information or your custom requirements.